制造业工业4.0落地案例:AMR如何提升车间效率?
摘要
1 引言
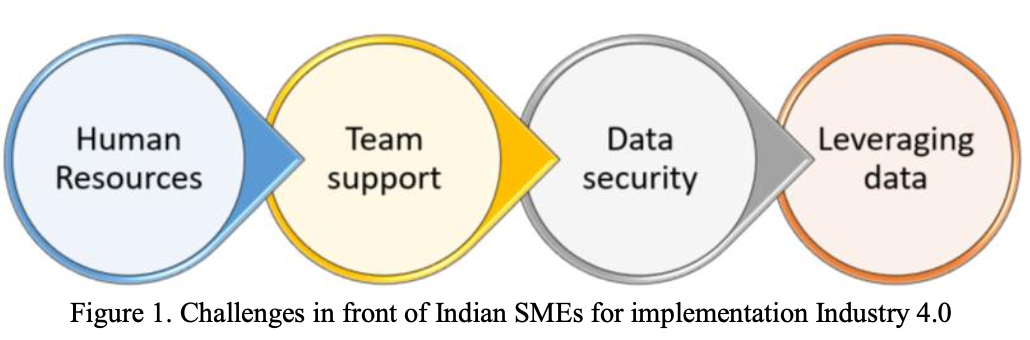
技术挑战——印度中小企业面临挑战,因为其内部缺乏必要的数据分析和IT培训专业知识。企业迫切需要一支能够管理I4.0技术的高素质人才队伍。此外,缺乏明确的I4.0实施模型和指导方案是一大显著障碍。不足的数字基础设施也使得I4.0技术的顺利整合变得困难,需要在连接能力和数据处理能力上进行显著提升。
财务障碍——将传统运营模式完全转型为数字化模式需要投入大量资金用于机械设备、云基础设施和法律成本。高昂的资本支出成为许多企业的阻碍因素。此外,规模化成本高企以及缺乏资源和知识支持规模化,对中小企业构成了严峻的财务挑战。
监管与政策障碍——企业面临法律合规性问题以及缺乏支持性的监管环境。制定明确的I4.0实施指南和框架对于缓解法律不确定性至关重要。政府在提供激励措施、补贴及营造有利政策环境方面的作用,对减轻财务负担并推动I4.0技术应用尤为关键。
因此,通过文献综述可知,组织内实施I4.0是一个复杂的过程,需对企业当前状态、战略目标和可用技术有深入理解。尽管关于I4.0的研究日益增多,但缺乏针对具体实施路径的详细指导。早期研究主要聚焦于理论层面,如I4.0的原则、技术、优势与障碍。尽管这些研究对建立基础认知至关重要,但未来需更关注企业可落地的实践洞察与行动步骤。因此,本文以车间智能物料搬运为例,展示AMR的实施过程,以满足日益增长的生产需求和灵活性。时间研究帮助确定所需的AMR车辆数量,成本分析则验证了该替代方案的有效性。叉车与AMR的OPEX和CAPEX模型对商业决策起到关键作用。
2 制造业中的AMR
AMR一直是机器人领域的研究与开发重点。它们可在无需持续人工干预的环境下自主移动并执行任务。AMR因其在工业、服务和物流场景中提升效率与生产力的潜力而受到广泛关注。
2017年,约69,000套物流系统被部署,其中包含约7,000台应用于制造环境的AGV,占当年专业服务机器人出货量的63%。到2021年,估计另有600,000台设备被部署用于生产内外的物流场景。这一增长得益于AI和ML等先进技术的融合,使AMR能够智能决策并适应动态环境,从而显著提升其效能与可靠性。此外,AMR市场按载重能力细分,从100公斤以下至2001-5000+公斤以上,广泛应用于电子、半导体、汽车、制药、医疗保健、物流及食品饮料等行业。
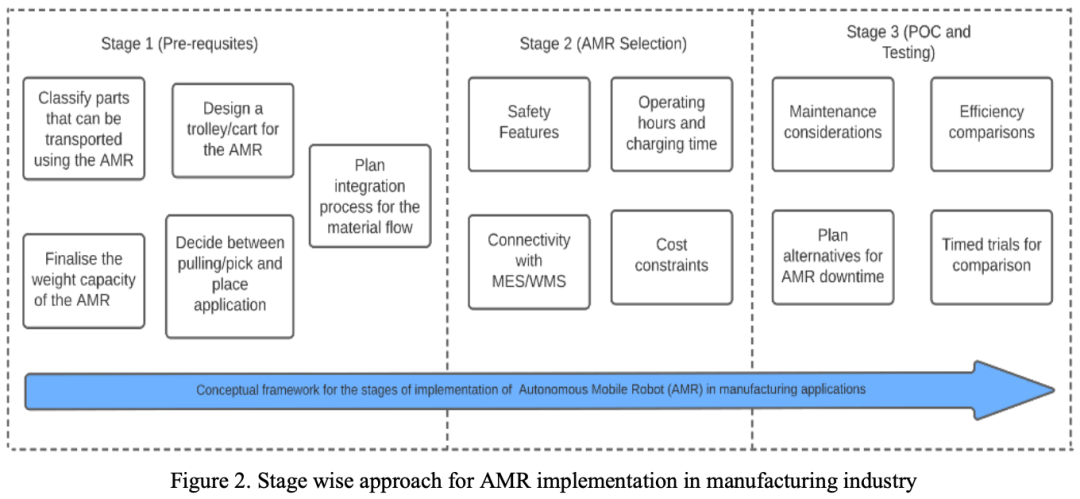
生产制造对灵活性的需求日益增长。机器人技术、AI和自动化等新技术,以及精益制造等组织方法正受到重视,以消除制造流程中的冗余环节。以下步骤为实施这些变革提供了路线图:
识别需运输物料的类型及数量
实施计划的第一步是根据AMR(如组件、子装配件、成品或生产过程中使用的其他物料)对需运输的物料进行分类。AMR能够执行设施内部的库存与产品运输,承担对产品或运营附加价值较低或无附加价值的低技能任务。它们可接收、分拣并将产品运送至指定位置,适用于输送机间的物料转运、拣选与发货操作中的产品排序,以及订单托盘化。AMR适用于动态环境及包含不同库存SKU的操作场景,也适用于“人到货”和“货到人”的物流操作。
一旦明确需运输的物料类型,即可基于具体的运输需求选择合适的AMR类型。物料分类需依据其尺寸、重量、数量及装配线所需物料的频次,需对物料特性进行详细分析。例如,小型轻质物料可能需要小型化AMR,而大型重质物料则需要负载能力更高、结构更坚固的AMR。物料重量是确定AMR载荷能力的关键因素,重物运输需依赖具备相应举升和承载能力的AMR,以确保制造环境中的运输安全与效率。物料搬运中AMR的分类因素如图3所示。
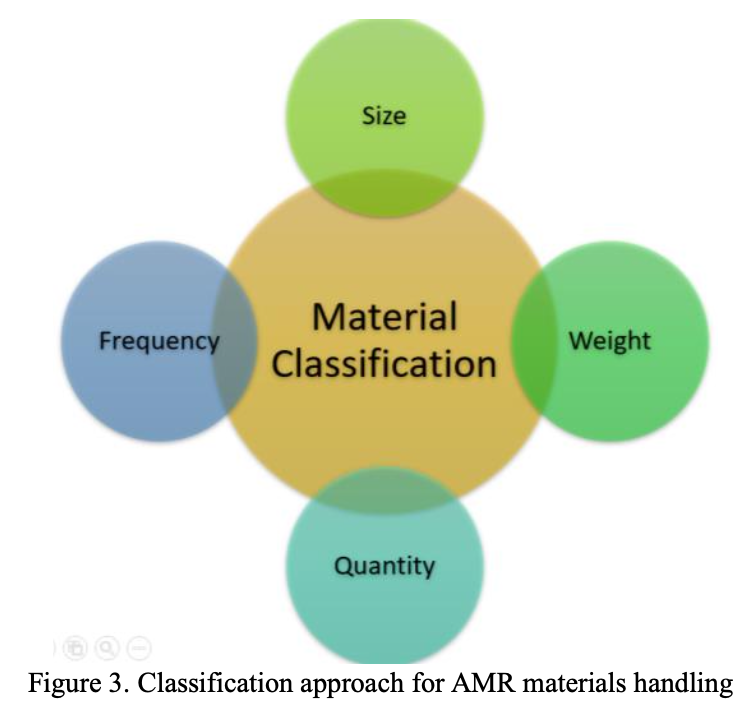
AMRs具备协同作业的能力,可高效处理大规模物料运输需求,其多机协作逻辑会根据生产流程中的具体物料量进行动态优化。AMRs的调度与路径规划受物料进出产线频率的影响,依据物料需求的紧急程度,可选择连续/按需运输模式或定时运输模式。通过基于这些因素对物料进行精细化分类,实施团队能够更科学地决策AMRs在制造工厂中的选型、配置及部署方案,从而实现AMRs与物料搬运流程的高效无缝整合。
设计拖车/推车适配牵引型AMR
当AMR需要执行牵引作业时,设计专用拖车/推车至关重要。该装置作为AMR与物料之间的连接枢纽,需确保传输过程的安全性与效率。拖车/推车必须与所用AMR的具体型号兼容,其尺寸规格、载重能力及连接机构需与AMR性能参数匹配,以保障运输过程的稳定性与安全性。设计时需充分考虑牵引力等动态载荷对结构强度的影响,确保装置具备足够的耐用性。
对接现有物料流系统
为实现AMRs与传统人工搬运方式的高效融合,需综合评估多重要素以确保系统级集成的流畅性。AMRs与人工物料处理技术的协同整合是提升整体运营效率的关键,需通过同步化方式将AMRs嵌入现有物料流体系,使其能与叉车、牵引车、堆垛机等人工设备无缝交互。具体实施需绘制完整的物料流动路径图,明确AMRs与人工设备的交接点位,并制定严格的安全规范与通信协议,确保人机共存环境下的作业安全。
AMRs需通过互联的系统架构与传统人工设备协同运作,例如接收来自叉车、牵引车等设备的实时位置与物料状态数据,同时向人工操作端反馈进度信息。系统设计应具备应对制造场景中物料流变动的适应能力,支持AMRs在突发延误、交接点变更或路径偏移等异常情况下的动态调整。这种灵活性通过搭载先进软件及控制系统实现,可基于物料可用性、人工设备位置及生产计划动态分配AMRs任务,最终在保障安全与通信效率的前提下,通过任务优化提升整体物料流的响应速度与运营效能。典型车间场景应用的AMR示意图见图4。
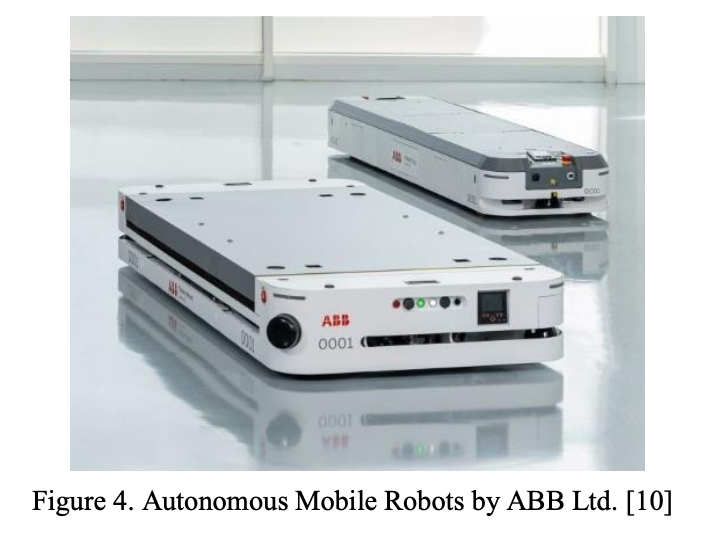
IT与系统集成
AMR应能与MES和WMS无缝集成,以确保制造流程各环节之间顺畅通信与协调。
REST API是AMR与MES/WMS系统集成的常用方法。REST API允许AMR接收物料流的实时更新,并据此调整路径规划。该协议易于使用,可适配多种现有基础设施。ZeroMQ是一种轻量且高效的通信协议,可快速便捷地在AMR与其他系统间传输数据,为AMR与WMS、ERP等外部程序交互提供灵活的方式。DDS是一种通过高速网络实现实时信息交换的协议,适用于需要实时共享大量数据(如视频和传感器读数)的AMR场景。OPC-UA是一种机器人应用软件开发协议,通过提供标准化平台实现降本增效并简化集成过程。
传感器接口:AMR配备多种传感器(如LiDAR、摄像头和超声波传感器),用于检测路径中的障碍物和人员。AMR集成急停按钮和人工干预系统,可在紧急或潜在危险情况下由操作员手动停止机器人运行。安全级LiDAR系统:此类系统提供360度视野,使AMR能够检测人员或车辆的存在并采取避障措施。
安全合规性:AMR需符合ISO 3691-4:2023和ANSI R15.08等安全标准,这些标准为AGV及AMR的安全使用提供指导。
概念验证与AMR停机测试
制定AMR离线时的应急方案对维持制造效率至关重要,需综合考虑多种技术因素。部署备用AMR可最大限度减少因故障或损坏导致的中断,这些备用机器人可编程接管物料搬运任务,确保主AMR失效时无缝衔接。若AMR停机,可通过人工方式(如叉车或堆垛机)保障物料流连续性。部署AMR车队管理软件可显著提升机器人性能并减少停机时间,该软件具备状态监控、问题诊断和维护任务调度功能。另一种替代充电方案是更换电池,可保持AMR持续运行。通过解决上述技术问题,企业可制定有效的AMR停机应对策略,保障物料处理流程顺畅运行。此外,还可基于多种技术因素分析AMR与传统方式(如叉车或牵引车)的效率差异。
3 方法论
研究人员在一家制造企业开展案例研究,该企业认识到自动化与工业4.0的重要性,对机器人技术进行了重大投入。为满足需双班生产的制造需求,企业将物料搬运流程自动化列为重点任务,旨在缩短制造周期、优化成本并拥抱新技术以推动增长。尽管员工流动率较高,企业仍优先安排受训人员从事高价值工作(如操作先进设备),并投入资源确保物料追溯精确性和库存优化,减少人工操作导致的错误(如货物检验失误或物品错放)。
研究对象为工厂内涉及物料搬运的4个主要区域:(1) 仓库,(2) 手推车区,(3) 生产区,(4) 测试区(参见图6)。工厂使用小型电动牵引车将物料手推车从仓库运送至车间,并将组装成品转移至测试区。适用解决方案为AMR。研究通过对比时间效率、成本效益及安全提升、工厂系统互联等无形收益进行评估。
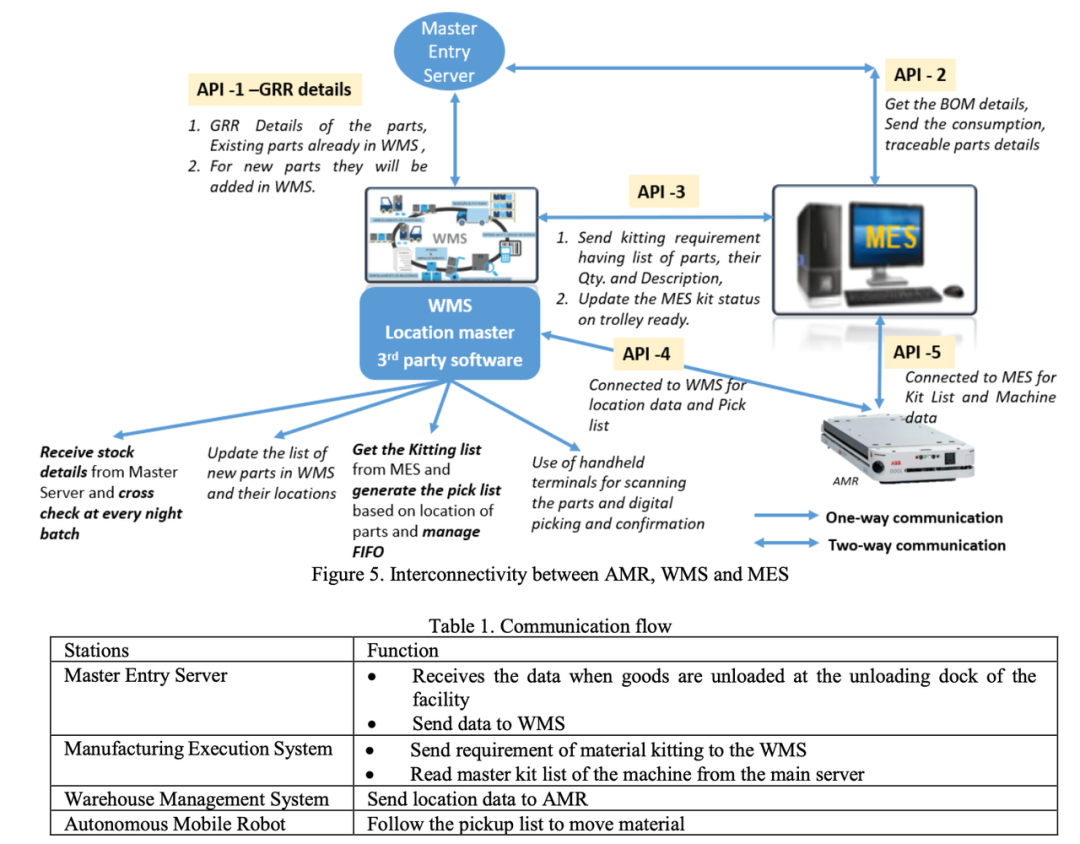
图5展示了AMR、WMS与MES之间的操作通信流程。制造设施中连接系统的数据流主要涉及主入口服务器、MES、WMS以及最终的AMR。所有关键单元的功能已列于表1中。主入口服务器在货物卸载至设施卸货码头时接收数据,随后通过API-1将包含零件详情及数量的信息发送至WMS。这些零件会被添加至库存,并根据可用空间分配至仓库特定位置。设施通过主服务器接收新客户订单,主服务器存储所有机器的BOM及配置信息。当接收到新订单时,该机器的BOM会通过API-2发送至MES,MES根据生产主管为不同阶段制定的生产计划生成车间物料需求。MES再通过API-3将物料配给需求发送至WMS。WMS已基于现有数据生成拣选清单,并遵循FIFO协议。当各阶段物料准备好并装载至手推车后,系统会向MES发送信号,MES再向AMR系统发送物料需求指令。AMR通过API-5与MES连接,通过API-4与WMS连接,从WMS获取位置数据并遵循物料拣选清单。仓库操作员将物料装入手推车后,AMR将物料运送至车间所需工位,这一过程通过系统互联节省了大量时间。
4 结果与讨论
为更好地决策是否以AMR替代传统物料搬运系统,开展了全面的时间与成本研究。
通过对比现有系统与建议系统的平均单次运输距离及运输次数,分析时间效率。运输任务分为三个主要类别——车间至仓库(蓝色)、仓库至车间(红色)及车间至测试区(黑色)。图6展示了该流动模式,表2列举了示例任务的时间统计。
仓库至车间:此阶段需先将货物从仓库运送至手推车区域,由操作员按制造流程整理物料并装入手推车,随后将物料运送至车间进行组装。
车间至仓库/手推车区域:空物料手推车随后被送回手推车区域重新装载,以延续循环流程。
车间至测试区:组装完成的货物将被运送至测试区进行测试与质量检查。
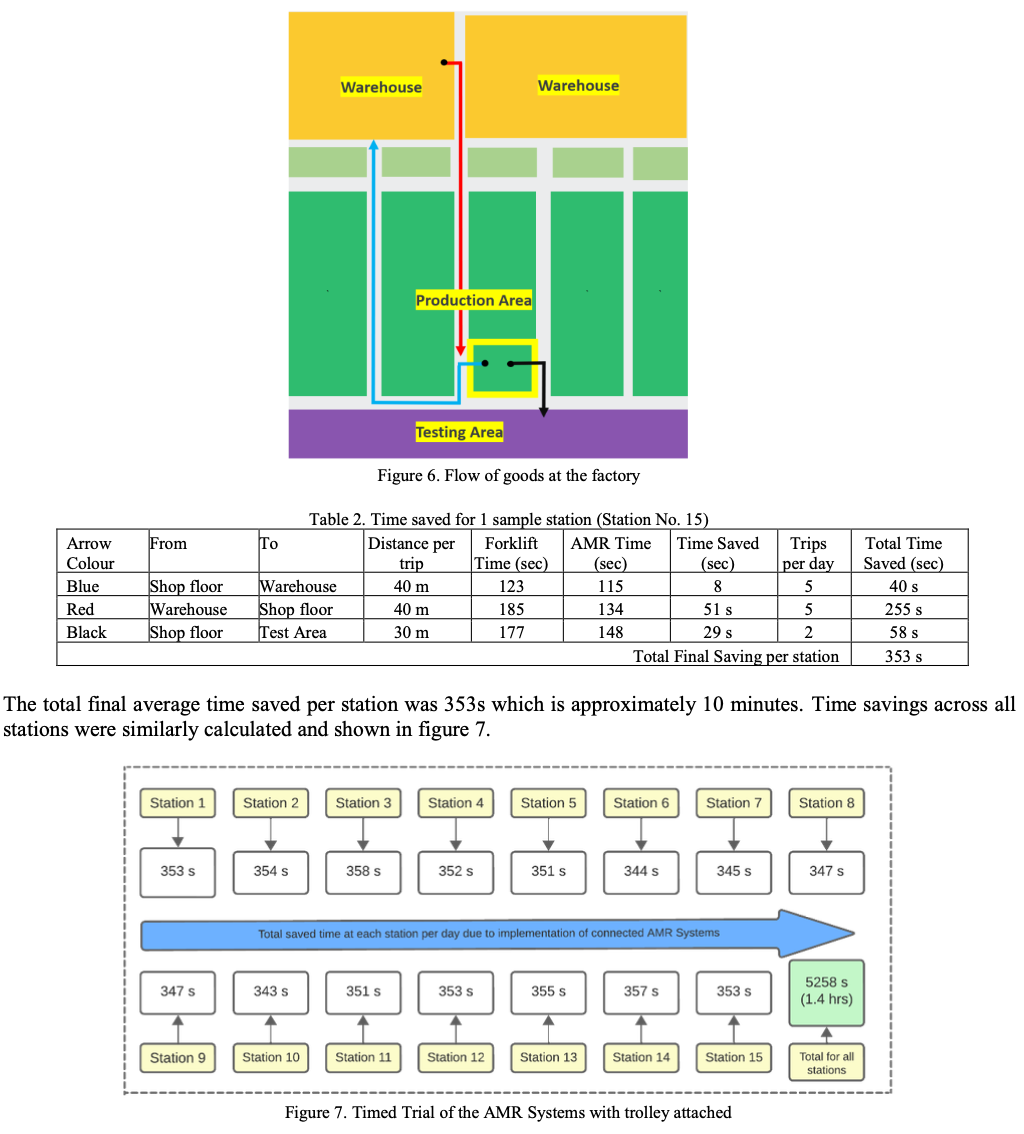
根据总计算和测试结果,所有工站合并计算的物料搬运至生产线的总耗时减少了约1.4小时。节省的时间主要来自于零件定位和位置导航所需时间的减少。与人工驾驶者相比,AMR系统可直接导航至预设位置。编程至导航系统中的路径优化技术有助于减少物料流动所需时间。在此案例中,多个因素如停机时间、生产中断被视为独立变量。由于无论使用何种物料搬运设备(MHE),停机时间均可通过考虑备用方案轻松应对。另一个被考虑的因素是MES-WMS-AMR之间的互联互通。这大大提升了零件交付时效及零件的可追溯性。
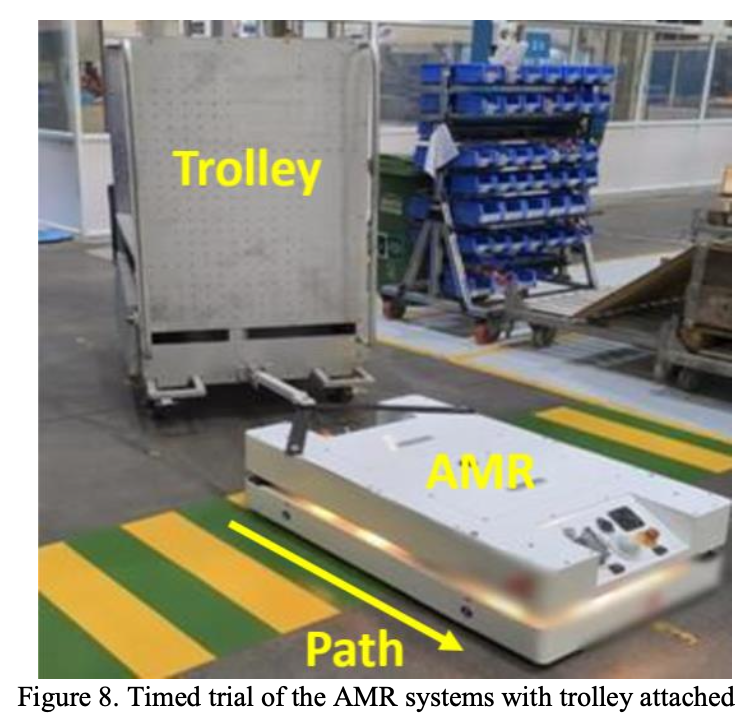
在实施此类系统时应实现的主要优势之一是其相关的成本效益。AMR的一个核心特点在于执行任务时所需的人工监督更少。一名工程师可同时控制多台AMR,从而实现成本效益与安全性并存。另一方面,每台拖车操作员均需配备一名人工驾驶员,进而增加相关成本。AMR的初期投资属于CAPEX,涉及购买或租赁机器人本体及相关基础设施(如充电站或导航系统)。此类支出将计入资产负债表并在机器人使用寿命内进行折旧。而AMR运行和维护的持续成本(包括电力、维护及任何必要的软件更新)则属于OPEX。尽管CAPEX反映了向自主系统转型的前期投入,但OPEX则涵盖了利用和维护这些机器人所产生的日常运营费用。通过仔细评估OPEX与CAPEX,企业可就采用AMR做出明智决策,在初始成本与潜在长期运营效率及成本节约之间取得平衡。表3列出了叉车与AMR成本分析的基本输入参数,即资本支出部分 。
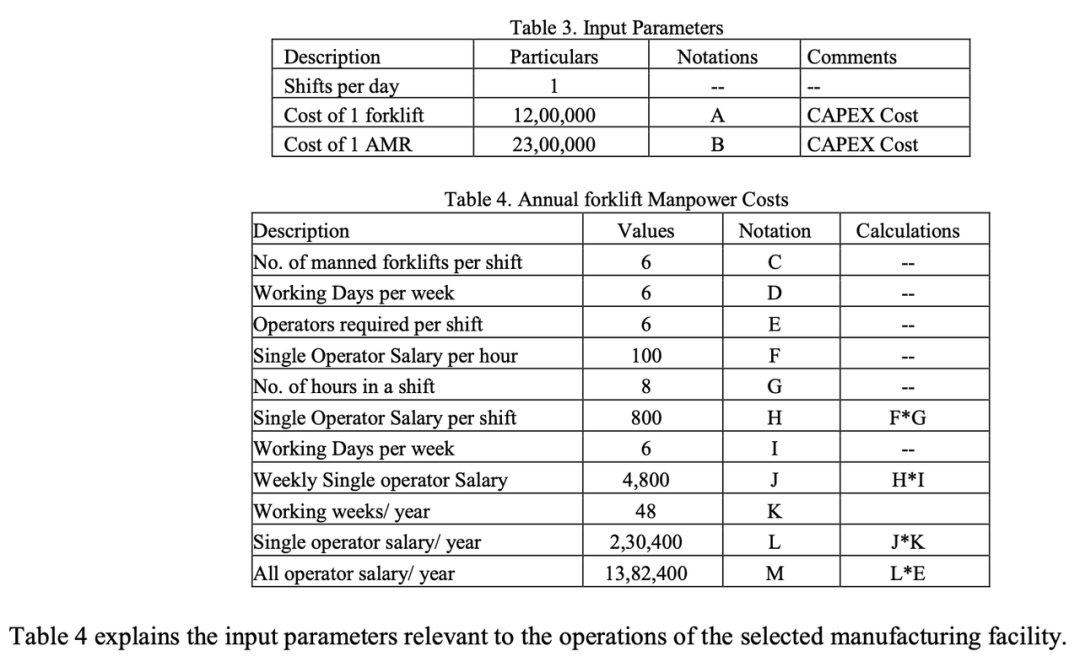

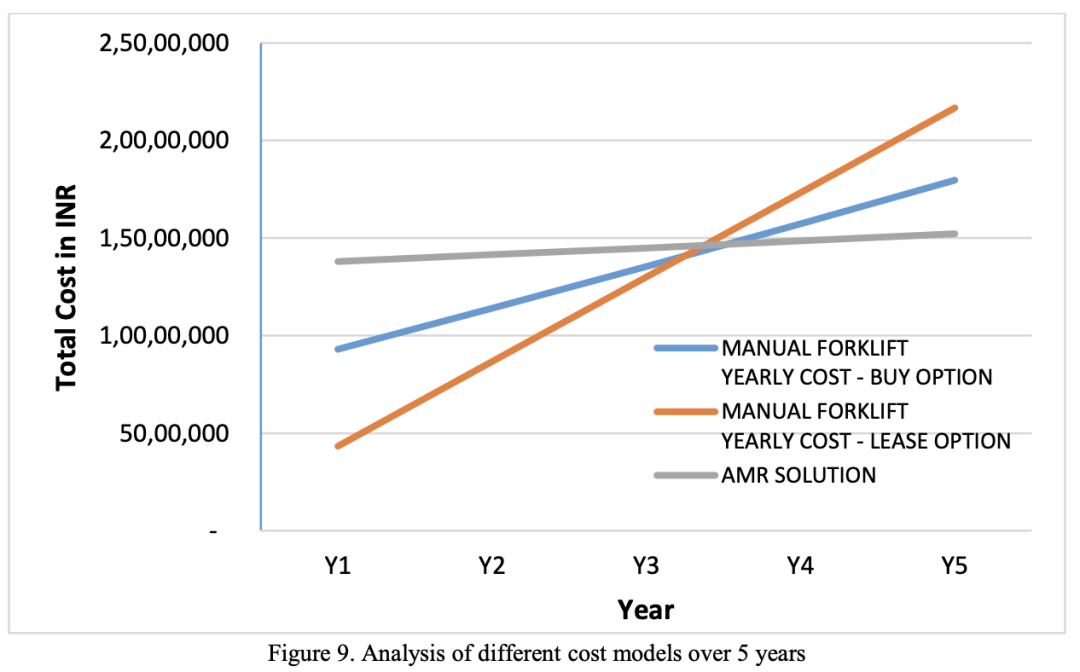
上述结果是通过对拖车与AMR在物料搬运方面的移动研究进行详细比较而得出的。通过速度、定时测试等多种因素计算物料搬运所需时间。本研究论文通过分析制造业实施I4.0相关的机遇与挑战,为持续探讨I4.0及其对制造业转型的潜力贡献了实践洞见,并提供了可帮助企业利用数字化力量实现效率与创新新高度的实用见解。本文综合考虑了制造企业在实施过程中可能面临的障碍,并提出了相应的解决方案与实施路径。研究识别了企业在I4.0实践应用中的研究空白,强调了对I4.0实际实施细节提供明确指导的必要性。文中讨论的实施阶段将帮助组织做出科学决策,提升其适应制造业快速变革与技术进步的能力。作为I4.0实施的一部分,AMR系统的实施优势已在图10中对比总结。
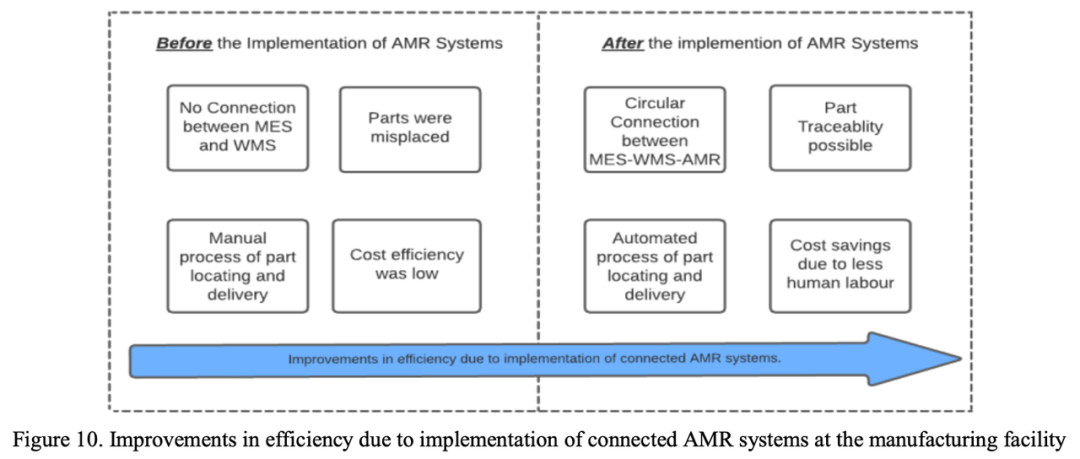
5 结论
组织在实施各类技术先进项目时可能面临的最终问题是证明初始投资成本的合理性。在此情境下,组织需明确初始投资的合理性可通过有形与无形两种形式体现。
• 本研究有效提出了基于API的主入口服务器通信模型,涵盖MES、WMS及AMR系统。
• 替换决策的时间研究显示,在15个站点中节省了343-358秒的时间,平均节省353秒,总计节省1.4小时(5258秒),其中仓库环节实现了最大的时间节省。
• 在所研究的3种成本模型中,AMR的CAPEX模型在5年成本分析中比其他模型节省约30%的成本。
• 详细的OPEX与CAPEX分析支持将6台叉车替换为6台AMR,其中5台用于常规操作,1台作为停机及充电期间的备用设备。
为支持该项目,必须识别关键绩效指标与运营指标、制定目标架构、规划所有措施的实施,并开展I4.0评估。通过遵循上述策略并提交结构清晰的商业提案,企业可对I4.0创新的资源分配作出科学决策。未来可进一步研究如何使技术更具备可行性,以帮助组织合理论证初始投资。
参考文献
S, Garrido, J. Muniz and V. Batista Ribeiro, “Operations Management, Sustainability & Industry 5.0: A critical analysis and future agenda”, Cleaner Logistics and Supply Chain, Vol. 10, pp. 100141, March 2024 https://doi.org/10.1016/j.clscn.2024.100141.
A. Sama, L. Hendric, H. Prabowo, Meyliana and A. N. Hidayanto, “Acquiring Automation and Control Data in The Manufacturing Industry: A Systematic Review”, Procedia Computer Science, Vol. 227, pp.214–222, November 2023 https://doi.org/10.1016/j.procs.2023.10.519.
R. Kler, P. A. Nimmagadda, D. Chauhan, and G. R. Babu, “Recognition and implementation of the smart manufacturing systems in industrial sectors for evolving industry 4.0” Measurement: Sensors, Vol. 31, pp.100987. February 2024 https://doi.org/10.1016/j.measen.2023.100987.
G. Fragapane, R. de Koster, F. Sgarbossa, and J. O. Strandhagen, “Planning and control of autonomous mobile robots for intralogistics: Literature review and research agenda”, European Journal of Operational Research, Vol. 294, No. 2, October https://doi.org/10.1016/j.ejor.2021.01.019.
M. F. Arroyabe, C. F. A. Arranz, I. F. Arroyabe, and J. C. B. Arroyabe, “The effect of IT security issues on the
implementation of industry 4.0 in SMEs: Barriers and challenges”, Technological Forecasting and Social Change, Vol. 199,pp. 123051, February 2024. https://doi.org/10.1016/j.techfore.2023.123051.
K. Govindan, and G. Arampatzis, “A framework to measure readiness and barriers for the implementation of Industry 4.0: A case approach”, Electronic Commerce Research and Applications, Vol. 59, pp. 101249, June 2023.https://doi.org/10.1016/j.elerap.2023.101249.
M. Braglia, R. Gabbrielli, L. Marrazzini, and L. Padellini, “Key Performance Indicators and Industry 4.0 – A structured approach for monitoring the implementation of digital technologies”, Procedia Computer Science, Vol. 200, pp.1626–1635,March 2022. https://doi.org/10.1016/j.procs.2022.01.363.
Industrial robotics Insights into the sector’s future growth dynamics, McKinsey & Company.(https://www.mckinsey.com/~/media/mckinsey/industries/advanced%20electronics/our%20insights/growth%20dynamics%20in%20industrial%20robotics/industrial-robotics-insights-into-the-sectors-future-growth-dynamics.ashx accessed on January 2025).
A. F. Costa, M. do S. Carvalho, M. Henriques, and P. V. Ferreira, “Strategy for the introduction of autonomous driving technologies: a case study in the logistics area of an automotive company”, Procedia Computer Science, Vol. 204, pp.337–345, September 2022. https://doi.org/10.1016/j.procs.2022.08.041.
Autonomous Mobile Robots (AMRs), Robotics. (2023)...(https://new.abb.com/products/robotics/robots/autonomous-mobile-robots accessed in January 2025).
D. Niermann, C. Petzoldt, and M. Freitag, “Intuitive and Flexible Process Control for Autonomous Mobile Robots: A Case Study in a Large Logistics Enterprise”, Procedia CIRP, Vol. 120, pp.153–158. January 2024
https://doi.org/10.1016/j.procir.2023.08.028.
G. Buchgeher, B. Dorninger, C. Klammer, A. Walchshofer, and A. Kern, “Migrating Cyber-Physical Systems to OPC UA”,Procedia computer science, Vol. 200, pp.276–283, March 2022.https://doi.org/10.1016/j.procs.2022.01.226.
13. ISO. (2023). ISO 3691-4:2023. (https://www.iso.org/standard/83545.html Accessed 14 Apr. 2024).
Dr. Dattatray Hulwan is an Associate Professor and Head of Mechanical Engineering Department. His research
interests include harnessing solar energy, thermal engineering etc.
Dr. Avadhoot Rajurkar is an Assistant Professor in Mechanical Engineering Department. His research interests include advanced manufacturing processes, robotics and automation, soft computing.
Mr. Adwait Gaikwad has been student from Mechanical Engineering Department and project intern on this project.
TsingtaoAI通过对前沿先进具身机器人与协作机器人的算法和智能体开发,搭建面向自动化工厂的具身智能实训平台,可以让企业在实际大规模产线决策建设前,进行预研实训,以让企业获得更快接入超级AI工厂的能力。
TsingtaoAI基于PBL的项目式实训理念,自研基于DeepSeek的具身智能实训解决方案、LLM的AIGC应用开发实训平台、基于LLM大模型的AI通识素养课数字人助手、一站式机器学习/深度学习/大模型AI训练实训平台和基于大语言模型的AIGC案例学习平台,为央国企、上市公司、外资企业、政府部门和高校提供AI&具身智能实训道场建设服务。